|
Perfection
of a New Generation
All the
ETA range of boilers are built to an exacting standard using the highest
quality materials matched with second to none Austrian Engineering. The
ETA PE range of domestic pellet boilers are designed with ease of use,
efficiency and safety as priorities.
1.
Automatic Filling:
The PE boiler uses a vacuum turbine to automatically load pellets from the
main pellet store as required. The boiler is connected to the main store by
flexible vacuum hoses, the boiler can suck pellets up to a maximum distance
of 20 meters. There is a 60kg day hopper built into the boiler from where
pellets are fed, as required, to the burning chamber.
2.
Advanced Pellet Feeding: The boiler has an advanced pellet feeding system that takes pellets
from the day hopper to the burning chamber in a measured and safe manner. The
system has a built in rotary valve that prevents any burn back from the fire
into the pellet store.
|
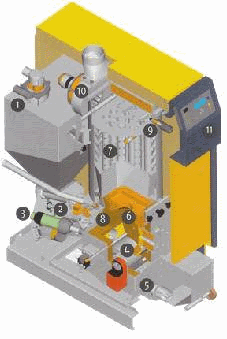 |
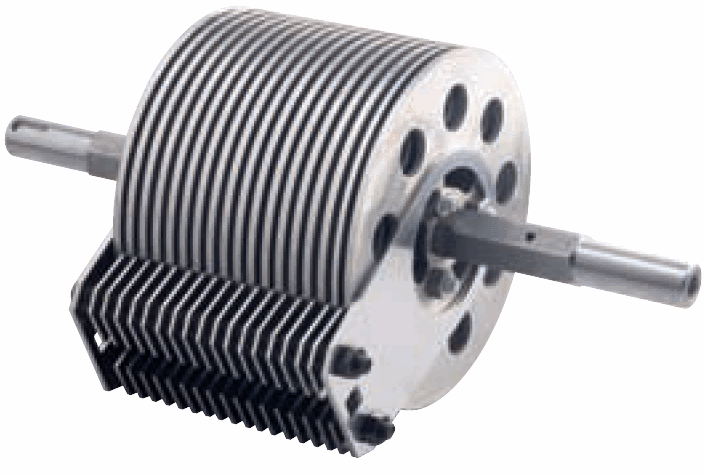
|
3.
Automatic Ignition:
With an ETA PE there is no messing around with matches and pieces of paper,
when the building needs heat the boiler burns, when it does not the boilers
switches off.
4.
Rotary Grate:
This device (patented by ETA), allows continuous de-ashing during combustion.
Pellets burn on the rotating grate, as it turns the grate removes ashes and
introduces air directly to the fire bed. This means highly efficient use of
fuel with pure fertilizer left in your ash bin
|
5. Ash
Removal: Automatic
ash removal from the combustion chamber to the ash box.
6. Complete Combustion: Top of the range technology ensures that the
combustion chamber always gives complete combustion of the wood pellets with
miniscule emissions in the exhaust.
7. Dew Point Safe Heat Exchanger: Automatic daily cleaning ensures
that there are always optimal conditions available to achieve the best
burning efficiencies.
8. Thermal Mixing Valve: Allows flow temperatures vary from 30-85°
C
9. Lambda Probe: Continuous monitoring of the O2 content in the
exhaust allows the boiler to adjust burning conditions, as required, to suit
changing fuel quality.
10. Quite Draught Fan: The
draught fan on all PE models is practically inaudible; a feedback loop to the
control panel ensures that there is always negative pressure in the
combustion chamber.
11.
Complete Regulation: An intelligent system allows remote operation, zone & hot water
tank control and weather compensated heating
|
Advanced
Feed System
ETA have designed their feed system to be efficient, safe, robust and easy to
maintain.
Metering
Screw: The
metering screw removes pellets from the day hopper. Every time the screw
turns the CPU is able to calculate how many pellets have been used. From the
control panel can tell you, in kgs, how much fuel is being used.
Rotary
Valve: The rotary
valve is fed by the metering screw with pellets, the reason that the rotary
valve is not placed directly under the day hopper is to prevent wear on the
valve edges that is caused by pellets get stuck there.
|
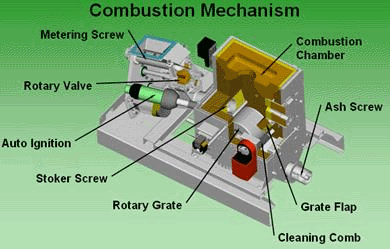 |
The
rotary valve is the fire break between the pellet store and combustion
chamber and as follows; Pellets are dropped into rotary valve chambers at the
top by the metering screw. The wheel turns around and drops the pellets into
the stoker screw, thereby keeping solid brass between possible fire and the
pellet hopper at all times.
Auto-Ignition: The
ignition fan operates by blowing compressed air over an electric heating
element, similar to the way an electric paint stripper works. Wood pellets
require 200°C to ignite, if required the ignition fan can provide air at
650°C
Stoker
Screw: The stoker
screw pushes pellets, received from the rotary valve, into the combustion
chamber where the pellets are ignited and burnt
Rotary
Grate: Pellets
from the stoker screw are burnt on top of the rotary grate, continuous grate
movement means the fire bed is always being riddled and fed with plenty of
air – thus allowing for a full and clean burn of the fuel.
Cleaning Comb: The
cleaning comb fits in between the gaps in the rotary grate, continuously
cleaning the grate as it turns.
Grate
Flap: Each day as
the heat exchanger cleans itself the soot is dropped on top of the rotary
grate, during the process the grate flap opens while the rotary grate rotates
in the opposite to normal direction allowing the soot to be dropped on top of
the ash screw.
Ash Screw:
This auger comes
on during cleaning to push all ashes and soot into the ash bin at the front
of the boiler
Combustion
Chamber: The
combustion chamber is lined with precision made refractory blocks, this
allows the flame to burn up to 1200°C without damage the chassis of the
boiler
|
Safety
First:
Safety is top
priority at ETA and in the 15 years that ETA have been producing biomass
boilers there has not be a single reporting of any boilers catching fire in
the field. This is not by chance, ETA engineers and designers have spent many
long days ensuring that all their products are safely designed and safely
manufactured.
Negative
Pressure:
A draught
fan on the outlet of the boiler exhaust pipe ensures that there is always
negative pressure in the burning chamber. Positive pressure can lead to
explosive burn back along the feed system and is one of the main areas that
boilers with front mounted draught fans fall down. In the event that the draught
fan fails there are sensors to tell the CPU to shut down all air valves and
put out the fire.
|
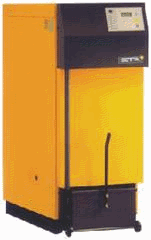 |
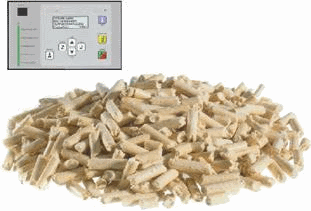 |
Rotary
Valve:
The
rotary valve in the feed system place a solid piece of brass between the
burning chamber and the day hopper creating an air tight seal. There is no
need for water based fire extinguishers to be penalised on this boiler
Fire Break in Main Hopper:
In the
unlikely event that fire does make it back to your main pellet store along
the suction pipes, there is a fire break placed in the front of the
extraction auger. Any fire in this area will cause expanding foam to block
the path of fire into the main hopper. We have never seen one of these
deployed!!
|
Boiler
Sensors:
The
boiler has many sensors built in, including the following; Boiler Temp,
Exhaust Temp, Flow Temp, Negative Pressure in Burning Chamber, O2 Content,
Flow Temperature, etc. If any of these readings starts going out of normal
operating condition then the boiler will make moves to correct it –
failing this the boiler will shut down.
|
Design:
The
combustion chamber, combined with the ETA rotary grate and automatic cleaning
process ensure the existence of the basic conditions, at all times, required
to create a consistent, long lasting fire. This results in low ash
accumulation, high burn efficiency and unusually low emission values. The
screw beneath the combustion chamber automatically removes ash into the ash
box.
Consistency:
The exhaust fan causes a constant negative pressure in the boiler and
therefore ensures high working reliability at all times.
Complete
Control:
The ETA PE boiler provides as standard, complete regulation of functions
such as combustion air, speed of draught fan, fuel feed,
accumulator tank management, hot water storage tank monitoring
and circulating pumps control.
|
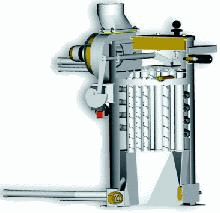 |
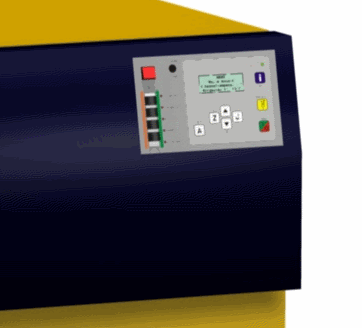 |
All
extended control modules are connected through the ETA control BUS.
Similar to the way ETA regulates it's own heating system (e.g. boiler,
accumulator, etc) you can add as an optional extra an external control module
that will allow you to integrate more heating circuits or regulate a second oil
/ gas-fired boiler and solar collectors (for heating water) so that
they operate seamlessly in a combined heating relationship with the ETA
boiler.
Regulation:
- Heat
adjustment through accurate proportioning of fuel and air
- Automatic
igniting of boiler whenever heat is required
- Combustion
is regulated by the Lambda probe to provide a clean burn with a long and
lasting heat efficiency
- Remote
controlled heat control from inside your house
- Prioritise
where you want the heat to go, e.g. hot water storage tank
- Rotary
valve and stoker screw make sure that only the correct amount of pellets
are burnt
- Monitoring
of the entire boiler through the VDU with plain simple language
- External
communication with the boiler though the ETA control BUS, allowing
integration of extra heating circuits, temperature sensors, solar
collectors and even other boilers
|
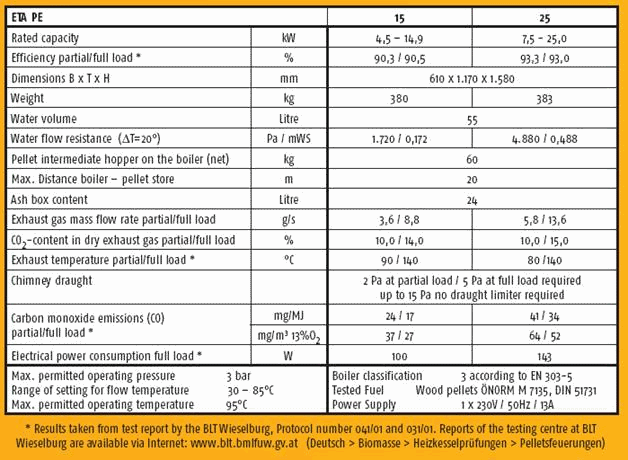
|
|