|
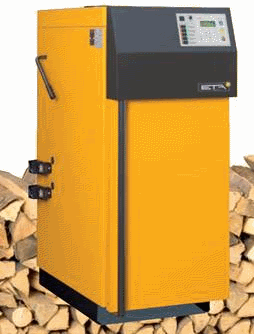
|
How
does the wood gasification boiler work?
Wood
gasification
Before
wood can burn, it must be converted into gas by applying heat. At 100°C
the water contained in the wood escapes. At 200°C the material decomposes
into 20% charcoal and 80% wood gas, a mixture of carbon dioxide, carbon
monoxide, hydrogen, methane, methanol, various phenols, acetone and acetic
acid. 400°C suffice for outgassing, but at least 900°C – better
1,100°C – are required to completely break up the phenols (wood
tar) into combustible carbon, carbon monoxide and hydrogen. In addition to a
high temperature, complex compounds take time to break up, which explains the
long gas flame of a wood fire.
Large
woodpile in fuel chamber
At the
foot of the woodpile in the fuel chamber a small gasification fire is
maintained with controlled air intake (primary air). The boiler electronics
regulate the gasification rate via the primary air intake The wood gas is
extracted downwards into a hot combustion chamber. This prevents the woodpile
in the fuel chamber from outgassing in an uncontrolled manner and igniting. A
boiler with a large wood capacity, slow burn-up and long burning period is
thus possible.
|
Mixing
jet and complete swirl
A mixing
jet is located between the fuel chamber and combustion chamber. At this point
pre-heated combustion air (secondary air) is added to the wood gas. The flame
from the mixing jet is ejected at high speed onto the hot floor of the
combustion chamber and is once again whirled around (4) to ensure that every
combustible gas particle encounters sufficient oxygen for complete combustion.
|
Complete
combustion in the glow zone
To
achieve an uncooled combustion at high temperatures, the patented glow zone
combustion chamber is made of high refractory bricks and is additionally
thermally insulated. In this glow zone the flame has sufficient time until
the last stubborn carbon rings (phenols) break out of the lignin of the wood
and burn at temperatures of between 900 and 1,200°C. ETA have thus
succeeded in remaining below the magical limit of 100 mg/MJ carbon monoxide
emissions in the flue gas of a wood boiler.
|
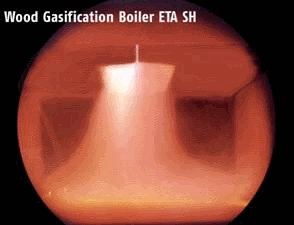
|
TECHNICAL
DESCRIPTION
The ETA
SH Wood Gasification boiler has an induced
draught ventilator for efficient firing of the fuel,
a large chamber (150 litres for SH 20/30 and 225
litres for SH 40/50/60 models) so that refueling
is reduced to once or twice a day. Complete
with a control panel including a timer for two
heating circuits. Approved by TÜV in Germany where the ETA SH has performed
top of the
class in its field in relation to lowest emissions
and highest degree of efficiency.
|
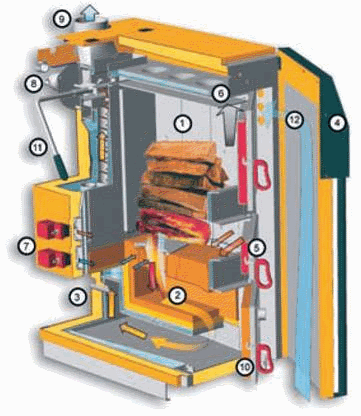
|
1.LARGE
FUEL FILLING SPACE: fuel capacity of 150 litres in the SH 20/30 models and
225 litres in the SH 40/50/60 models means that refueling intervals kept to
a maximum.
2. ZONE ISOLATED AND ANNEALED COMBUSTION CHAMBER: The combustion chamber is lined with a high temperature ceramic Fire Brick that is light and prevents
ash build up.
3. LAMBDA SENSOR: The SH boiler uses a lambda probe to adapt the firing
process to suit differing types of wood, it identifies the energy density of
the timber through the oxygen content of exhaust fumes and then adjusts the
burning process to suit.
4. EASY REGULATION: The control panel allows for easy, and accurate,
regulation of the boiler, buffers, water cylinders and circulating pumps.
5. RE-LIGHT WITHOUT MATCHES: When you refill the chamber with new fuel you don’t have to go messing about with
|
6.
GASIFICATION: Secondary burning of carbonised gas from the wood fuel
(normally lost to the atmosphere in the exhaust gas) reduces emissions and
ensures optimal usage of all wood fuel burned in the combustion chamber.Temperatures in the combustion chamber can reach up to 1200 °C as a result.
7. PRIMARY AND SECONDARY AIR ACTUATORS: The primary and secondary air valves have a regulated position feedback link to the main control panel; this
allows accurate and subtle control of primary and secondary combustion
whenever required.
8. SILENT COMPRESSOR: The boiler has a barely audible, step-less, regulated induction fan with speed feedback to the control panel. Max electrical power
consumption of the motor is 76W.
9. EXHAUST GASES: Seamless replacement of previous boilers due to monitored
exhaust gas temperature, feedback loop to control panel.
10. EASE OF REGULAR MAINTENANCE: Regular maintenance is easily done through the main front door, there is no need for extra side doors and hard to reach
hatches.
11. EASY CLEANING: the heat exchanger is the easiest of tasks, just pull the
shaker handle on the outside
|
BETTER
PERFORMANCE
For the
first time ever it is now possible to burn all forms of wood in the same
boiler, it doesn’t matter if it Ash, Spruce, Beech, Wood Briquettes or
even waste carpentry timber. The ETA SH boiler can burn all of these woods
efficiently while at the same time keeping it’s emissions with in the
boundaries of the magical carbon monoxide (CO) limit of 100mg/MJ. This
magical figure is achieved through the use of the ETA Lambda probe; the probe
measures the remaining oxygen particles in the boiler exhaust gases
continuously and then regulates the primary and secondary air induction to
match so that the boiler is always operating at the optimum level of
efficiency. In addition this system also makes sure that not too much air
enters the burning process, surplus air would draw heat from the boiler out
in the exhaust and thus reduce efficiency
|
SIMPLE
OPERATION AND NO NEED FOR MATCHES
To refill
the heating chamber you just open the door and load it with fresh timber or
wood briquette fuel. Due to the high load capacity of the chamber you only
have to refuel once or twice a day depending on outdoor temperature and house
size. Once the door is closed the firing stage begins using the remaining
embers to light the new fuel can be ignited automatically – you light
the fire manually the first time and the boiler will keep enough embers to
relight the fire for 24 hours (This only applies if you are burning hardwood
such as Ash, Beech, Oak, etc).
|
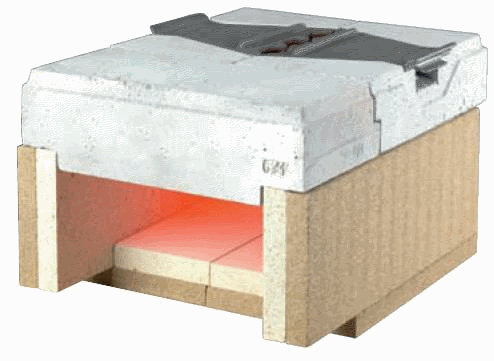 |
The lambda probe checks the oxygen content of the exhaust and adapts the
firing process to suit the fuel used, it identifies the energy density of the
timber in this manner adjusts the primary and secondary draughts to suit
varying levels of moisture content – thereby always giving the fuel
optimal burning conditions.
Before leaving the boiler room you just have to pull the lever on the side of
the unit to clean the heat exchanger in the boiler and you are done –
this ensures a high degree of efficiency at all times.
|
BETTER
THINKING
High
efficiency is the sum of innumerable details and ETA have gone into all the
details with this unit - for example, air that is used for combustion is
drawn along the gap between the boiler panels and the internal boiler so as
to reduce the amount of heat lost from the boiler through radiation resulting
in an extremely low 0.78% of heat lost through radiation including floor
loss.
BETTER
HEAT
Since
combustion air is tightly controlled, there is no excess air to cool the
fire, as a result the ETA combustion chamber burns between 1000 and 1200°
C. Combustion chambers in conventional wood burners do not have the
durability to withstand such heat, whereas the ETA multipart combustion
chamber is made from a stable high temperature ceramic material with built in
expansion joints.
|
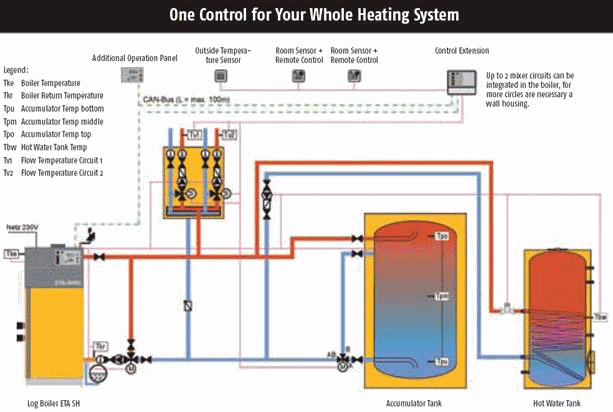
|
|